Machines in mining depend on pressure. They bear a heavy load by being utilized in high loads, severe conditions, and a long work period. That’s what makes good maintenance not merely a good idea but a matter of survival.
Even with the best equipment in the world, without a good maintenance schedule, it can break down. Emergency breaks can sometimes result in long down times and massive losses.
These are all necessary steps addressing reliability, speed, and economy. In this article we want to discuss the 3 must-do activities for maintenance of heavy equipment that secure (to some extent) long term machine reliability for your mining operation.
Inspections Must Be Carried Out Every Day
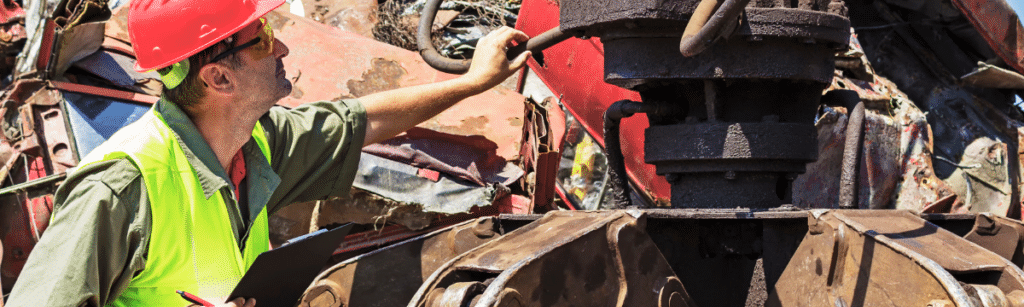
It might sound routine, but it is crucial to be checking every day. Before each work shift, operators should perform a pre-shift equipment inspection. Begin with simple things — fluid levels, tire pressure, and hydraulic systems.
Check for signs of wear, rust or leaking. Listen out for unusual sounds and vibrations. These are often early signs of trouble. Maintaining checklists can be useful to monitor trends. Small things can snowball over time.
Regular notes allow your team to get out ahead of your account. The more inspections you perform, the less often you get hit with surprise failures. Even carving out 10 minutes a day can save hours of downtime later.
Training also matters. Make sure all operators are aware of what to check. Teach them to report problems the right way. Provide them with a system to flag violations on the spot. When everyone follows the same recipe, the results can improve.
Follow A Schedule Of Preventive Maintenance
Machines don’t come cheap and running them until they break is costly. This is what preventive maintenance helps us steer clear of. That covers scheduled oil changes, Part replacements, Filter swaps, and more.
The aim is to put a halt to breakdowns before they begin. What Every Piece Of Equipment Should Have: A Schedule. Follow the instructions included in the manufacturers’ manual.
Tweak the plan based on real-world data. For instance, a loader in moisture, will require more regular maintenance. Track dates and tasks with software. Timely reminders help the team keep a schedule.
Also, check your schedule frequently. If you see repeated failures, change the plan. Your machines talk and talk and talk through their data. The closer you listen, the better your results will be.
Condition Monitoring Should Not Be Neglected
Condition monitoring uses the run-time health checks of a machine. Some are sensors that record the temperature, vibration, noise and oil quality. These small readings can serve as an early warning for big problems.
The second process is cheaper and takes less time. It’s not guesswork, and its sights are set on actual problems. Why tear down a running engine “just to check.” You intercede only when the data tells you to.
The starting point is to mount sensors on important bits — engines, gearboxes, hydraulics. Integrate them into a unified dashboard. Set alert limits. If someone steps over the line, your team can act quickly.
Condition monitoring services complement preventive strategies. Collectively, they form a clever system. Machines run smoother. Heavy equipment maintenance solutions become focused.
Establish A Soild Maintenance Culture
Machines aren’t going to fix themselves. People do. That’s why culture matters. A vigorous culture of maintenance makes caring a form of the quest for virtue. It starts from the top. Leaders need to make maintenance.
Train all employees, not only the mechanics. Operators, supervisors and even planners should know how the machines work. Early warning signs are everyone’s business to identify. Educate people to speak up when they see changes.
Incentivize teams to cut down on breakdowns. Celebrate your inspection worksheet is clean as hell and that you made it work order free. This builds an ownership pride. People who feel culpable act faster and act smarter.
When maintenance becomes a way of life, everything gets better. Machines last longer. Failures drop. Oh, and your team has more confidence in addressing issues early.
Conclusion
Mining machinery is subjected to tremendous strain every day. But if you do things correctly, then they do last long term. Preventive maintenance is when you stop failure before it starts!
Condition monitoring allows for instantaneous knowledge. And a strong culture keeps your team centered and accountable. “It’s more of a package deal — all of these different things work best when they’re used together,” she said.
They minimize downtime and save money, contributing to smooth running processes. Ultimately, preventive maintenance saves both your machines and your bank account. Follow these habits, and your mining operation will be able to keep at it for years to come.
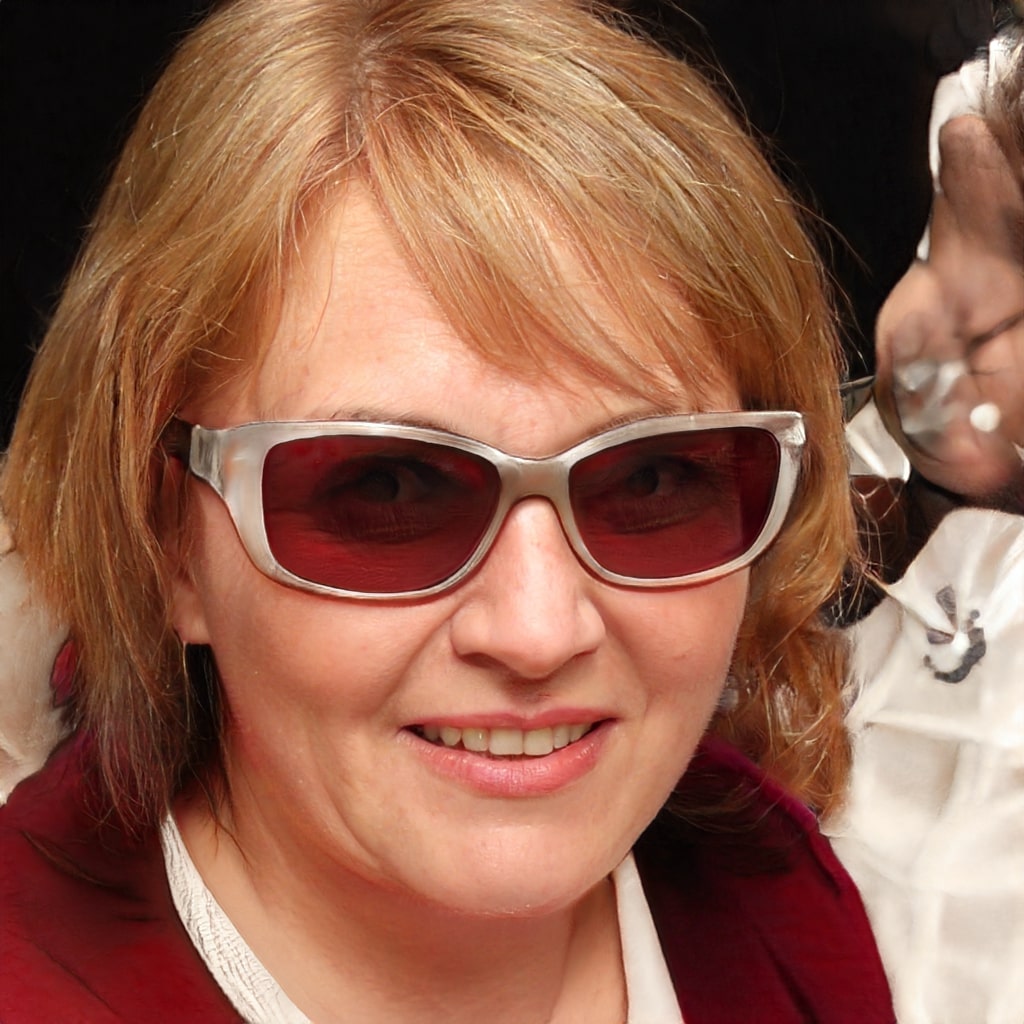